Les Laboratoires de structures et de matériaux composites apportent des changements à la construction aéronautique – et aux éléments utilisés.
Par Phillip Trum
Un bon avion doit être assez solide pour supporter des vents furieux, assez léger pour se maintenir dans les airs et assez résistant au feu pour ne pas s’enflammer. Imaginez maintenant une nouvelle génération de matériaux de construction aérospatiale présentant toutes ces caractéristiques, et plus encore. Ces matériaux seraient peut-être aussi conducteurs d’électricité, éliminant ainsi des kilomètres de fils électriques. Peut-être seraient-ils également capables de détecter, et de signaler, qu’ils sont endommagés, voire de changer la forme même des avions.
Pascal Hubert, professeur agrégé en génie mécanique et membre des Laboratoires de structures et de matériaux composites, contribue à la mise au point de ces matériaux composites qui poseront les bases du programme Aviation 2.0. Les composites sont faits à partir de résine (comme le polymère) renforcée par une fibre (comme la fibre de carbone). Contrairement à l’acier, par exemple, qui est fait d’un mélange homogène de fer et de carbone, les divers constituants du matériau composite peuvent être produits par ingénierie de façon à être dotés de propriétés destinées à une application particulière. Les concepteurs de cellules d’avion peuvent ainsi optimiser leur travail en éliminant le poids excédentaire, ce qui permet d’accroître les économies de carburant, le rayon de vol et la capacité marchande. Les composites ont aussi l’avantage de réduire le temps et les coûts de production (en plus du poids des pièces d’attache) en intégrant les petites pièces en une seule grande, qui ne nécessite aucun assemblage.
Titulaire de la Chaire de recherche du Canada en matériaux composites avancés, Pascal Hubert n’a entrepris des travaux dans ce domaine qu’à la fin des années 1980, la récession l’ayant forcé à abandonner ses recherches en aérospatiale. « Mon premier travail sur les matériaux composites a porté sur quelque chose de très québécois », se souvient-il, « des chenilles de motoneige! » Comme il l’a rapidement appris, la production de matériaux composites était à l’époque un processus encore mal défini et à forte intensité de main-d’œuvre. Un bref détour dans l’industrie du bois d’ingénierie lui a ouvert les yeux. « J’ai alors compris dans quelle direction il fallait se diriger ; nous avions besoin d’une plus grande automatisation et d’une meilleure compréhension du traitement des composites. Nous aidons maintenant les entreprises à développer une approche davantage scientifique, alors que nous procédions auparavant par tâtonnement. »
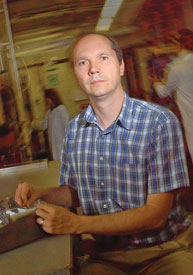
L’un des projets en aérospatiale que mènent actuellement les Laboratoires de structures et de matériaux composites, sous la direction de Larry Lessard, professeur agrégé au Département de génie mécanique, allie à la fois l’intelligence industrielle et universitaire grâce à la collaboration de Bell Helicopter Canada, de Delastek inc., de l’École polytechnique de Montréal, du Centre des technologies de fabrication en aérospatiale du Conseil national de recherches du Canada et du Consortium de recherche et d’innovation en aérospatiale au Québec. Le projet a pour but de concevoir un bec de bord d’attaque stabilisateur en fibre de carbone époxy, destiné à l’empennage horizontal d’un hélicoptère, et qui peut être fabriqué à l’aide du procédé de moulage par transfert de résine (MTR). De tels becs sont habituellement assemblés à partir de plusieurs pièces d’aluminium; le bec monopièce obtenu par MTR réduira vraisemblablement le temps et les coûts de main-d’œuvre, en plus d’être un produit fini plus solide. « Une bonne partie de notre recherche porte sur la compréhension du procédé de fabrication du matériau composite, ainsi que sur l’effet du procédé sur la performance finale du matériau », précise le Pr Hubert.
Tout en mettant la dernière main aux réglages de précision du procédé de fabrication du matériau composite, le Pr Hubert et ses collègues des Laboratoires préparent aussi l’avenir. Mitsubishi et Honda fabriquent déjà des jets d’affaires entièrement faits de matériaux composites, et le produit à surveiller est le prochain Boeing 787. Surnommé « Dreamliner », cet appareil de moyenne capacité sera le premier avion civil d’envergure dont le fuselage et les ailes seront entièrement faits à partir de matériaux composites, au moment de sa mise en service en 2009. L’avion sera constitué de près de 60 pour cent de matériaux composites pour ce qui est du poids (par comparaison, un Airbus 320 en compte environ 20 pour cent), ce qui en fait un avion plus léger qui consommera au-delà de 20 pour cent moins de carburant.
« Nous devons songer au développement de la prochaine génération », souligne le Pr Hubert. « Le mot à la mode en ce moment est multifonctionnel. Lorsqu’on parle d’une structure, on désigne quelque chose qui sert à supporter des charges ou des forces provenant de l’environnement. Dans le cas d’un avion, il s’agit de la portance, de la traînée et du poids de l’appareil. La structure sert alors uniquement à supporter les transferts de charges d’un endroit à l’autre. Or, une structure multifonctionnelle pourrait exécuter d’autres tâches à la fois. Un avion, par exemple, est constitué de la structure en elle-même, mais aussi de kilomètres de fils électriques. Et si on pouvait concevoir une structure également conductrice d’électricité? Ou encore une structure pouvant détecter les dommages éventuels et signaler ce qui doit être réparé? Une grande partie du développement porte sur les matériaux aptes à remplir ces autres fonctions ».
On pourrait même envisager de recourir à la technologie de « morphose » afin de transformer la forme des ailes selon la configuration de vol. « Nous en sommes au point où l’on doit repenser la façon dont on conçoit la structure des aéronefs. Quand on s’y arrête, on constate que leur structure n’a pas beaucoup évolué au fil des ans, et ce constat vaut tout autant pour le fuselage, les ailes, etc. Lorsqu’on introduit un nouveau matériau composite, il arrive souvent qu’on ne tire pas avantage de ses propriétés, car il coûterait trop cher d’en modifier la conception. Nous construisons donc les mêmes structures, en ne remplaçant que les matériaux. Notre but est de mettre au point de meilleurs outils analytiques qui nous aideront à concevoir à partir de ces nouveaux matériaux. Nous souhaitons également élaborer des outils d’optimisation qui nous permettent d’établir la meilleure configuration possible sur le plan du poids et du coût. »
Parmi les sources de financement ayant permis la mise sur pied des Laboratoires de structures et de matériaux composites, mentionnons le Conseil de recherches en sciences naturelles et en génie du Canada, le Fonds québécois de la recherche sur la nature et les technologies, la Fondation canadienne pour l’innovation, le Consortium de recherche et d’innovation en aérospatiale au Québec, AUTO21 (un réseau de centres d’excellence), Bombardier, Bell Helicopter Canada et Delastek inc.