Sylviane Duval
Converting waste matter into biofuel is one thing. Building machines that can efficiently use these new fuels is quite another. Researchers in McGill’s Alternative Fuels Lab are working on getting the next generation of engines off the ground.
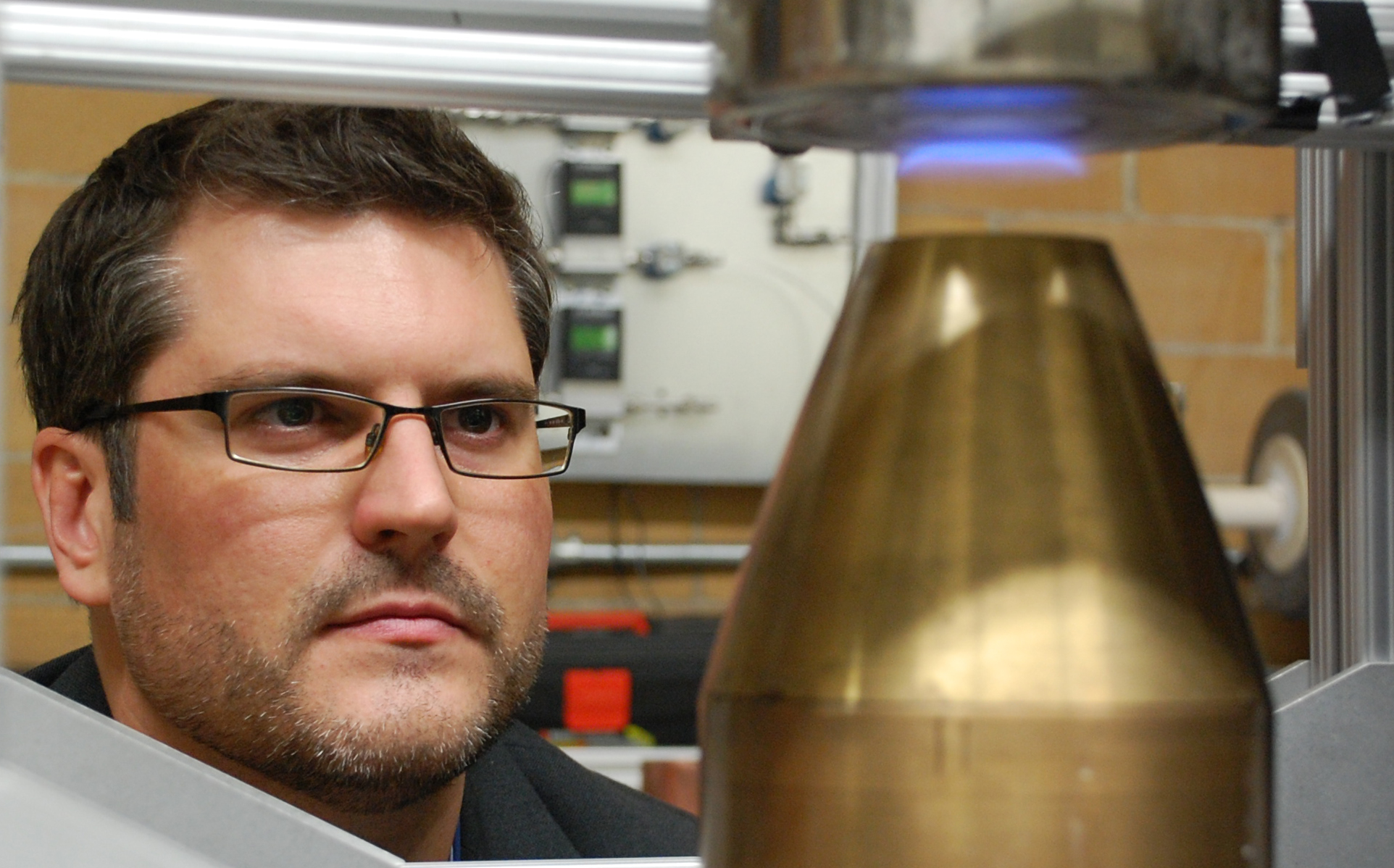
The Macdonald Engineering Building infamously burned to the ground in 1907. But now, over a century later, nobody minds that Jeffrey Bergthorson and his team like to play with fire in the safe confines of their newly renovated lab on the building’s first floor. The researchers carefully blend the right mix of fuel and air to create small, flat flames about three centimetres in diameter. Then they use laser diagnostics to probe the combustion chemistry of different fuels. These flames are the Number One apparatus of the Alternative Fuels Lab.
The Number Two apparatus is no less unexpected: a tube containing a mix of fuel and oxidizer through which they blast a shock wave that raises the temperature of the fuel so it catches light. With this, they measure the time it takes for the mixture to ignite.
“Nothing in here looks like a jet engine,” smiles Bergthorson, who is an assistant professor in the Department of Mechanical Engineering. “But these apparatus allow us to study the fundamental principles that precede engine design.”
Bergthorson is part of a cross-Canada team, led by McGill plant science professor and Green Crop Network director Don Smith, that’s working on developing new kinds of fuel and the engines that can burn them. The project, called Canadian Research Integration and Innovation in Biofuels Sustainability (CRIIBS) is one of the short-list finalists in the Government of Canada’s 2012 Networks of Centres of Excellence competition, which supports promising collaboration between researchers and industry. (The winner of this significant funding will be announced in the spring.) Instead of processing crops that could be used for food, they’re developing ways to turn waste, such as wheat straw, corn stover (leaves and stalks) or even wood salvaged from demolished buildings, into fuel. (Growing crops aren’t out of the picture entirely though: CRIIBS is also looking at the energy potential of “purpose-grown biomass”—things such as willow trees or fast-growing grasses that aren’t edible and don’t require prime agricultural land.) Bergthorson’s expertise, however, is in the combustion, not the creation, end of things: Once you’ve created a biofuel, how does it burn? And how can engine design be tweaked to get a bigger waste-into-energy bang for the buck?
When Bergthorson was completing his PhD at Caltech during the early 2000s, the “burning” questions in aerospace technology related to advanced high-speed propulsion and, therefore, combustion. Before turning his attention to how alternative fuels might benefit the commercial aviation industry, he studied supersonic combustion for hypersonic aircraft.
Jet fuel is strictly regulated. It must meet strict standards for energy content per litre, composition, viscosity, surface tension and other physical and chemical properties — tough criteria that make it impossible to use oxygen-containing biofuels such as ethanol or first generation biodiesel in aircraft. As well, the industry has put its foot down on the stratospheric cost of retooling the fuel supply system at airports and upgrading the global airline fleet for non-compatible fuels.
The combustion engine isn’t going away. “Renewable source or otherwise, jet fuel has got to be a hydrocarbon similar to petrofuel,” says Bergthorson. “There aren’t any disruptive technologies because nothing else has the high power-to-weight ratio or the necessary energy density. Hydrogen takes up too much space, and the power density of batteries is too low. There isn’t going to be an electric jumbo jet.”
The question is not whether alternative fuels burn — we already know that any hydrocarbon burns in the heat and pressure of an engine. It is how they burn… the way their physical and chemical properties affect the performance of the engine…and what comes out of the proverbial tailpipe.
One issue is materials compatibility. Alcohol- or vegetable-oil-based biofuels, for example, are corrosive and can wreck rubber seals by changing the way they swell. (It’s serious business: The space shuttle Challenger tragedy was caused by rubber seal failure.) Another issue is physical properties. A biofuel with a different viscosity than petrofuel will spray into the engine differently, change how the fuel and air mix and, therefore, affect combustion. Both are problems for Bergthorson’s collaborators at other universities.
Bergthorson himself is experimenting with different blends of alternative fuels, to see what happens to the sequence of chemical reactions that converts fuel and air into carbon dioxide and water. This includes extinction behaviour (how easy it is to blow out the flame), flame speed and stability; type and quantity of emissions; fuel droplet evaporation; and reignition at low temperatures. The last point is crucially important for restarting the engine after a flameout incident at 30,000 feet.
However, lighting a small flame in a lab and kickstarting a jet engine on a runway are worlds apart. In between the two lie gas-turbine combustor experiments and the inherent complexities added by the fuel spray and evaporation processes. Instead of this, Bergthorson has adopted an experimental and modelling approach that allows him to assess the effect of industrially relevant turbulence levels on the flame without using an actual combustor — and without cramming a jet engine into his lab. The results will inform other research work to integrate alternative fuels into transportation and power generation systems and help develop new engine designs that improve efficiency and reduce emissions.
Soaring petroleum prices, concerns over climate change, European cap-and-trade schemes that affect airlines, and the International Air Transport Association’s goal to reduce its carbon footprint by 50 per cent by 2050 — it all adds up to very keen interest in research that explores bio-derived fuels that will keep costs and emissions down. Bergthorson is involved in several large scale collaborative efforts with industry. Pratt & Whitney Canada, for one, has called on him — as well as experts at Université Laval, Ryerson University, the National Research Council’s Gas Turbine Research Laboratory, the Indian Oil Company, and other partner organizations and universities in India — to investigate the performance of different biofuel and petrofuel blends.
“Synthetic kerosene has been approved for use in jet engines. It meets the fuel standards but, because it is made from gasified coal, its environmental footprint is worse than petrofuel,” says Bergthorson. “Bio-derived fuels are now being shown to be engine-compatible and carbon friendly. The industry is already certifying hydro-treated vegetable oils, thereby opening the doors for widespread adoption.”
Could we also see these blends at the neighbourhood gas station in the future? Bergthorson shakes his head.
“True, we could obtain fuels similar to gas or diesel from these processes,” he says. “But because they have to meet the standards for jet fuel, they need more processing and that leads to higher costs. There will be cheaper solutions for the gas tank than bio jet fuel.”
In another collaboration, Bergthorson is working with Rolls Royce Canada, five Canadian universities, and the National Research Council on novel fuels for gas-turbine engines.
Rolls Royce’s Energy Division converts aviation gas turbine engines into power-generation systems suitable for remote or off -shore uses or for peak power generation by replacing the combustor and other key parts.
“The first two things a customer cares about when buying an engine are cost and reliability,” says Bergthorson. “But increasingly, they are asking if they can burn this, that and the other fuel depending on what is available and what is cheapest.” The research on gaseous fuels (syngas or biogas blended with natural gas) and liquid fuels (biodiesel, alcohols and upgraded pyrolysis oils blended with petrodiesel) will provide data that will help Rolls Royce meet ever-tightening emissions standards for these engines. As a result, Rolls Royce will be in a better position to evaluate what alternative fuel mixtures will work in existing engines and what design changes can be made to next-generation engine combustors to allow further fuel flexibility.
The Alternative Fuels Lab is funded by NSERC, FQRNT, CFI, CRIAQ (Quebec Aerospace consortium), Pratt & Whitney, ISTP Canada, Quebec MDEIE, Rolls Royce Canada and MITACS.